Eliminating Integration Barriers in Robotic Systems with XBMCU
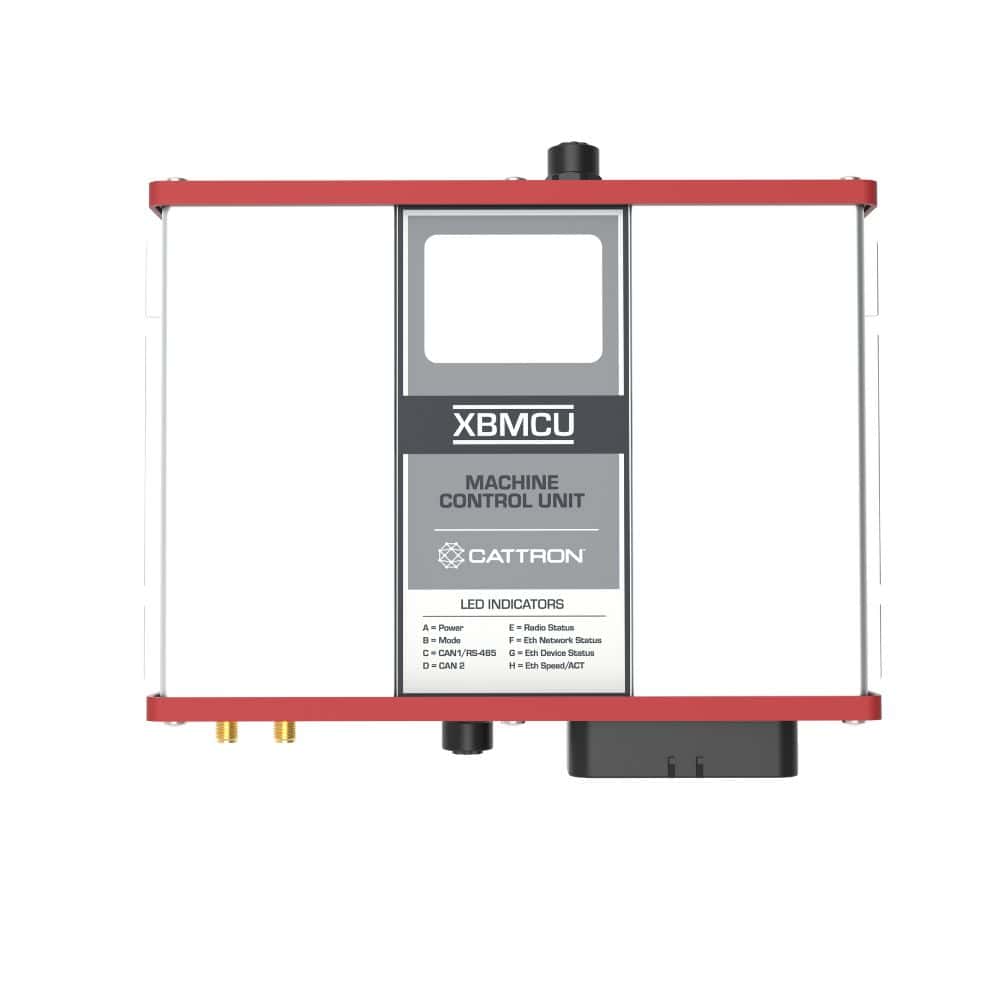
Robotic systems have revolutionized manufacturing across industries, yet a persistent challenge remains: optimizing integration processes and simplifying system maintenance. For system integrators, facility managers, OEMs, and maintenance teams, the complexity of connecting robotic systems with existing control architectures often creates costly delays and implementation challenges.
At Cattron™, we’ve addressed this challenge with the XBMCU Multi-Interface Machine Control Unit. This compact device fundamentally transforms how robotic systems integrate into industrial environments by supporting wireless control and monitoring through safe, encrypted RF communication combined with diverse serial protocol support.
The Integration Challenge in Robotics
For control engineers and machine builders implementing robotic solutions, historical challenges include the time and expense of traditional cabling required to bring valuable data and critical controls to end users. These dated methods not only cost time and money upfront to set up but require much more maintenance long-term, resulting in system downtime and additional costs to sustain operation.
“Application requirements are dictated by the machinery in use, existing communication systems, and industrial standards,” explains Mark Densley, sales leader at Cattron. “The XBMCU’s flexibility allows it to support industrial automation no matter the technology in place, benefiting both OEMs and end users with a singular product solution.”
Advanced Wireless Technology for Robotics
The XBMCU’s wireless functionality is provided by Cattron’s black channel, encrypted RF protocol. The unit serves as a gateway for machine data and control to safely travel over the air for a truly wireless solution with range support up to one kilometer.
This capability is particularly valuable for robotic applications, as the XBMCU takes data from the machine via traditional I/O or a customer PLC, converts it using a custom RF message structure with encryption, and broadcasts it to a variety of Cattron transmitters or another XBMCU in what is known as a machine-to-machine solution.
Cattron is a market leader in providing safe and reliable RF communication, and in combination with the advanced design of the XBMCU, represents the next era of wireless control for industrial automation integration. Specifically, the XBMCU’s machine-to-machine configuration acts as a bridge providing machine data and control in real-time, eliminating human response delays and taking the optimization of machine control and maintenance to an entirely different level.
Simplified Serial Integration
The XBMCU champions complex operations with a straightforward hardware interface. Setting up serial communication is as easy as connecting a PLC to the D-coded M12 connector. For safe protocols such as CANopen Safety, CIP Safety, and PROFIsafe, customers only need to add a power supply, and their machine is ready to go.
The unit supports a comprehensive range of protocols, including:
- Ethernet IP with future CIP Safety support
- PROFINET with PROFIsafe (currently under certification)
- Dual CANbus interfaces supporting J1939, CAN FD, CANope,n and CANopen Safety
This protocol flexibility enables the XBMCU to serve as a universal bridge between different robotic components, reducing system complexity and integration time.
Facilitating Robotic Safety Applications
Safety is paramount in robotic applications, and the XBMCU also delivers here. The core of the XBMCU product is designed and certified PL-d per the ISO 13849 standards. Beyond the hardware, the XBMCU has achieved several certifications with lab-tested and approved PROFINET and Ethernet/IP, and is in the process of TUV certification for PROFIsafe and CIP Safety.
The XBMCU works seamlessly with Cattron’s Safe-D-Stop™ wireless emergency stop system, enabling operators to carry portable e-stops with them as they work alongside robotic systems. This capability transforms the traditional stationary e-stop approach into a mobile safety solution that follows the operator, addressing a critical need in dynamic robotic work environments.
Machine-to-Machine Communication for Robotics
The XBMCU facilitates data-rich, bi-directional machine-to-machine communication that enhances robotic system performance. This connectivity enables:
- Seamless coordination between multiple robots
- Integration with existing PLC systems via serial protocols
- Real-time data exchange between robotic end-effectors and control systems
- Remote monitoring and control capabilities
This machine-to-machine configuration acts as a bridge, providing machine data and control in real-time, eliminating human response delays and taking robotic system optimization to a new level. The result is robotic systems that operate as cohesive units rather than isolated machines, maximizing efficiency and throughput.
Technical Specifications for Robotics Applications
The XBMCU’s technical capabilities make it ideal for demanding robotic applications:
- Eight digital inputs configurable for Category 3 PL-d
- Six 3A digital outputs configurable for Category 3 PL-d
- Wide range 9-36 VDC supply
- IP66-rated aluminum enclosure for harsh environments
- Lab-certified PROFINET communications with Class C Conformance
- Black channel wireless interface for secure communications
- Data logging capabilities for performance analysis
Practical Applications in Robotics
The XBMCU demonstrates significant value in several robotics applications:
AGV/AMR Control: The unit enables wireless control of autonomous vehicles through safe, encrypted RF communication with range support up to one kilometer, maintaining consistent connections even in challenging industrial environments.
Robotic Cell Automation: The XBMCU streamlines cell implementation and reduces maintenance requirements by facilitating communication between robotic arms and peripheral equipment with simplified connectivity.
Collaborative Robot Safety: The integration with Cattron’s Safe-D-Stop wireless e-stops enables enhanced safety protocols around collaborative robots, allowing operators to immediately halt operations from anywhere in the workspace.
Remote Operation: For hazardous environments or remote operations, the XBMCU enables operators to control robotic systems from safe distances using Cattron’s wireless transmitters.
Machine Tending: The unit simplifies the integration of robotic machine tending applications by reducing the complexity of connecting robots to the machines they service.
Transforming Robotics Implementation
The XBMCU is the wireless solution customers can rely on to improve their system operation and efficiency without compromising safety. The plug-and-play approach with simple M12 connectivity allows systems to be operational within minutes, dramatically improving implementation timelines and reducing engineering overhead.
For robotics integrators and end-users alike, this represents a paradigm shift in how automation solutions are deployed, maintained, and scaled. The XBMCU’s ability to work as an independent PLC while supporting multiple communication protocols makes it a versatile solution for virtually any robotic application.
The XBMCU offers robotics implementers a reliable, secure, and efficient path to enhanced automation without the traditional integration complexity that can delay implementation. For more information about implementing the XBMCU in robotic applications, contact us at [email protected].